The dry electrode coating course of has the potential to allow the manufacturing of higher, greener, less expensive batteries. It depends on superior fluoropolymer binders with Teflon
For a number of years now, Charged has been reporting on how dry electrode coating processes have the potential to revolutionize battery manufacturing by eliminating using hazardous, environmentally dangerous solvents. Taking the solvents out of the method can translate to large financial savings in price and flooring area within the manufacturing unit—and the dry coating course of also can allow designers to enhance battery efficiency.
The dry electrode coating course of depends on using particular binders that may type an electrode coating with out being dissolved in a solvent, resembling fluoropolymer binders with Teflon from specialty chemical firm Chemours.
To find out about the benefits of the dry coating course of, and the way corporations are assembly the challenges concerned in scaling the know-how up from pilot to manufacturing scale, Charged spoke with Tejas Upasani, World EV Expertise Supervisor at Chemours.
Tejas Upasani: We prefer to name Chemours “a startup firm with 200 years of historical past.” We spun out of DuPont in 2015, and we have now main manufacturers in varied industries, together with semiconductors and automotive. Below our Superior Efficiency Supplies enterprise, we have now manufacturers you may acknowledge, resembling Teflon, Nafion
and Viton
.
Now we’re experiencing development in our merchandise in a brand-new area—the dry electrode coating course of—and I’m actually excited to see how Chemours can help the scale-up of this new utility.
Within the dry course of, lots of the elements stay the identical—related energetic supplies, related conductive components. What actually adjustments is the binder.
Charged: Are you able to stroll us via the essential benefits of the dry electrode coating course of versus the standard moist slurry-based course of?
Tejas Upasani: The dry coating course of is a novel method of producing cathode and anode electrodes in lithium batteries.
Within the conventional moist slurry course of, we have now the energetic elements, we have now the conductive components, and we use a specific binder which must be dissolved in a solvent. As soon as all these elements are combined collectively, we create what is known as a slurry. That slurry needs to be coated onto a present collector. At that time, the operate of the solvent is finished, so we dry off the solvent and we get a pleasant coating on the present collector.
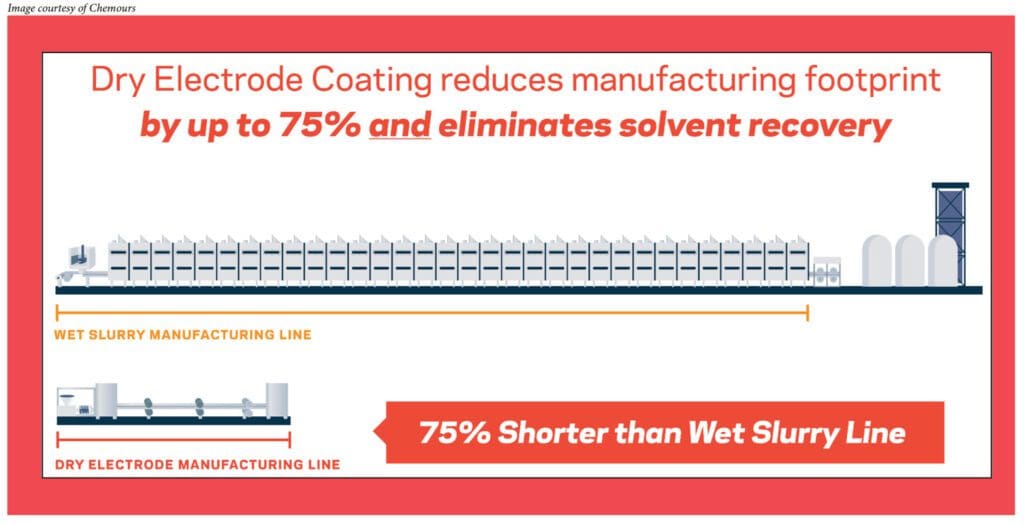
Within the dry course of, lots of the elements stay the identical—related energetic supplies, related conductive components. What actually adjustments is the binder. On this case, we’ll be utilizing superior fluoropolymer binders with Teflon which, due to its distinctive properties, doesn’t must be dissolved in any solvent. It could possibly type the coating because it goes via the processing steps via a course of known as fibrillation, which mainly types the complete coating on the present collector.
Why is the dry course of advantageous over the moist slurry course of? We are able to have a look at this from three completely different angles.
One is that it’s rather more environmentally pleasant. The moist slurry course of makes use of NMP [N-Methylpyrrolidone], which is a hazardous solvent. In an effort to do away with the solvent within the moist slurry course of, it has to undergo a collection of ovens. If there is no such thing as a want for the solvent, then the hazards related to the solvent are eliminated.
The second half is manufacturing prices. In case you have a look at how a lot area is required for the moist slurry course of, by some estimates, it’s 10 instances the area in comparison with the dry course of, so there’s an amazing quantity of financial savings of flooring area that may be achieved with the dry course of.
The third facet is that it permits higher efficiency of the batteries. With the dry course of, we will make thicker electrodes, which will help with bettering energy density.
Superior fluoropolymer binders from Chemours are actually on the coronary heart and middle of that course of.
Charged: Is that this one thing that might assist to scale back charging instances?
Tejas Upasani: It probably may. There’s a whole lot of testing that’s being carried out proper now, evaluating the moist slurry course of and the dry course of. If you’ll be able to go to a better loading with the dry electrode course of—say, all the way in which to eight or 9 milliamp-hours per sq. centimeter—we will see aggressive or larger charging charges in comparison with a traditional loading of the moist slurry course of, which is about 3 to 4 milliamp-hours per sq. centimeter now. A lot of this work is finished at lab scale or pilot scale, however because the know-how matures and we begin seeing higher course of applied sciences, these could be realized in real-life eventualities as properly.
Charged: Is dry electrode coating at the moment in manufacturing?
Tejas Upasani: We’re within the early phases of the event course of. Some {industry} gamers are at manufacturing scale. For instance, on Battery Day in 2020, Tesla introduced that they wished to provide their 4680 cells in a dry electrode course of. And on Investor Day in 2023, the corporate introduced that that they had efficiently carried out industrial manufacturing of the dry electrode course of. PowerCo, a subsidiary of Volkswagen, has introduced that they are going to deploy and commercialize the dry electrode course of at many various areas. LG Power Options has introduced related plans.
However because it stands proper now, we’re seeing the complete spectrum—lab, pilot, pre-production, manufacturing—of adoption of the dry electrode course of.
We predict that cell producers and OEMs within the subsequent two to 5 years are going to be in numerous phases. Some are going to be at pilot scale. Others are going to advance into manufacturing scale. However because it stands proper now, we’re seeing the complete spectrum—lab, pilot, pre-production, manufacturing—of adoption of the dry electrode course of.
Charged: Are there any main technical hurdles that we nonetheless must get previous earlier than this may be extensively adopted?
Tejas Upasani: Definitely there are hurdles. Everyone’s attempting to develop the method, and so they’re attempting to make it possible for the proper mixing and calendaring could be carried out in an effort to create a uniform construction. Among the technical hurdles must do with binders and the dry electrode processes enabled via understanding the fibril community of PTFE [polytetrafluoroethylene].
The usage of PTFE and the resultant fibril community has been understood for many years, and we, as inventors of PTFE, have invested a whole lot of science behind understanding the fibril community, nevertheless it typically has been utilized to industries the place PTFE is the dominant part within the utility. For instance, if you happen to have a look at your customary plumber’s tape (Teflon tape), it makes use of precisely the identical precept of fibrillation. That’s why you may pull it in a single path simply, however within the transverse path, you may simply break it aside.
It’s the identical on this utility—we’re attempting to regulate the fibrillation via the blending course of and thru the calendaring course of. Chemours has invested closely in creating varied sorts of superior fluoropolymer binders with PTFE. These have a variety of various molecular weights and completely different polymer architectures, and all of those are supposed to allow the correct fibrillation traits inside the electrode course of.
On the cathode facet, typically PTFE is oxidatively very secure…it’s a really promising utility. On the anode facet there is likely to be reductive stability challenges related to conventional PTFE, and so utilizing conventional PTFEs won’t be the optimum resolution.
Conventional PTFE might have challenges on the anode facet. On the cathode facet, typically PTFE is oxidatively very secure. One of many benefits is you can go to larger voltages and it nonetheless is secure at higher-voltage functions. So, on the cathode facet, it’s a really promising utility.
On the anode facet there is likely to be reductive stability challenges related to conventional PTFE, and so utilizing conventional PTFEs won’t be the optimum resolution. That’s one of many the reason why we’re creating a whole lot of completely different merchandise and attempting to know the mechanism of why conventional PTFE will not be secure on the anode facet. And as soon as we perceive that mechanism, how can we clear up that? There’s an amazing quantity of labor happening internally and with our exterior companions as properly to try to perceive and clear up these hurdles.
Charged: One of many challenges is adhesion. The dry materials has to bond to the electrode floor, however the flat floor and lack of texture could make that troublesome.
Tejas Upasani: The {industry} proper now could be utilizing what we name carbon-coated present collectors. They’ve sure coatings on the present collectors, and when the dry course of movies are made, these get laminated onto that carbon-coated present collector.
That’s the answer that the {industry} has at this level, and it’s working pretty properly in each anode and cathode processes. Now, if we wished to instantly laminate the movie onto the present collector with none carbon coating, then that’s a little bit little bit of an issue, and we’re engaged on it proper now.
We’re taking a look at ways in which we will alter the chemistry of the polymers themselves in an effort to get higher adhesion to the present collectors. If we have been in a position to instantly laminate onto the present collector, why have this carbon coating?
We’re taking a look at ways in which we will alter the chemistry of the polymers themselves in an effort to get higher adhesion to the present collectors. If we have been in a position to instantly laminate onto the present collector, why have this carbon coating? Eliminating the coating reduces the associated fee. I believe that may come, however proper now the main target is on scaling up the know-how with coated present collectors.
Charged: The method wants to scale back the quantity of binder and different inactive materials to the same degree as that of moist coating, however this may be costly and onerous to scale up.
Tejas Upasani: Yeah. Sure cell chemistries require growing the quantity of inactive materials, particularly on the cathode facet, whereas there are some cell chemistries the place we’re taking a look at binder loadings of lower than 2%, and in some circumstances even lower than 1%.
So, it’s already being labored on, attempting to scale back the quantity of inactive supplies. It does require a whole lot of course of optimization as a result of, as you may think about, the small quantity of binder is holding up the complete powder chemistry. So, a whole lot of course of know-how, together with the fabric enhancements that we’re doing in creating new supplies and developing with completely different polymer chemistries, goes to allow even additional reductions of the quantity of inactive supplies.
Charged: One other problem is uniformity—the dry coating combination must be uniform throughout giant areas of the battery electrodes.
Tejas Upasani: I don’t suppose uniformity challenges are essentially restricted to the dry coating course of. There are strategies which were developed within the moist slurry course of to know that the viscosity is correct or the solids content material is correct, and that can assist us to know that the uniformity of the slurry can be good.
As soon as the blending is finished homogeneously, the great thing about the dry electrode course of is that, as soon as it’s laminated onto the present collector, the coating course of is finished. You don’t have any motion or settling of the elements.
Within the dry course of, it’s related, besides that we’re coping with all of the powders. There are analytical strategies and instruments which might be being developed in an effort to confirm that these powders are combined appropriately—the energetic supplies, carbon black and binders, they must be combined actually homogeneously. As soon as the blending is finished homogeneously, the great thing about the dry electrode course of is that, as soon as it’s laminated onto the present collector, the coating course of is finished. You don’t have any motion or settling of the elements. In a moist slurry course of, if you happen to have been to make a thick electrode, because the solvent is drying off, these elements might begin to settle in the course of the drying course of.
Charged: So, your organization would associate with the producer to find out the best combine.
Tejas Upasani: Sure. And all through our historical past, we have now checked out utility improvement. That is what we have now carried out at Chemours for many years. We don’t need to simply say to the shoppers, “Right here’s a cloth, use it.” We don’t need to say that we’re only a provider. We don’t need to cease there. We need to make it possible for we contribute to the success of our clients as properly.
There are strategies obtainable to know the blending homogeneity, that are very R&D-based, and we’re doing a few of that work, but when somebody is doing this on a manufacturing foundation at a producing web site, they don’t seem to be going to have time to take a pattern, go into the R&D lab and look forward to days in an effort to get the outcomes. So, once we are creating these strategies internally, we try to develop a technique which goes to be consistent with manufacturing characterization and evaluation.
Charged: Are you able to inform us about your superior fluoropolymer binders with Teflon PTFE?
Tejas Upasani: Understanding the fibrillation traits is absolutely the important thing in enabling the dry electrode course of. We now have a spectrum of various merchandise, which can be found to be utilized in a batch mixing course of, or in a steady mixing course of. Not all of our clients are going to make use of the very same method of producing it, so attempting to tailor our merchandise to their wants is the important thing.
And on condition that we have now tried all differing types of chemistries for our superior fluoropolymer binder merchandise, it’s simpler for us to know what precisely goes to have an effect on the fibrillation traits, and consequently the mechanical properties of those supplies.
Additionally, Chemours is the one fluoropolymer producer who has manufacturing websites in all three main areas—the US, Europe and Asia/Pacific. Once we take into consideration a situation the place the manufacturing goes to be scaled as much as a manufacturing scale, we have now the pliability of getting the merchandise being made at completely different areas and supporting our clients with the identical high quality, the identical security requirements and identical requirements utilized to accountable manufacturing.
Charged: We’ve heard about some proposed rules in Europe round PFAS that might impression PTFE. What impression would this have on dry electrode coating?
Tejas Upasani: I’m glad that you simply requested the query, as a result of typically it’s the elephant within the room once we are speaking with our {industry} companions.
We at Chemours firmly consider that our fluoropolymers could be manufactured responsibly, and we’re in favor of industry-wide nationwide rules and testing necessities, that are based mostly on science and info—data-driven rules and testing strategies, we’re utterly in favor of that.
We spend a whole lot of time, cash and sources in figuring out the sources of emissions from manufacturing fluoropolymers, and putting in abatement programs in an effort to management these emissions. We’re additionally partaking closely in attempting to develop alternate manufacturing applied sciences. All of those are steps that we’re taking in an effort to meet the wants of potential regulation.
If we have a look at the EU rules, notably, it’s not essentially confined to PTFE. PVDF, which is a fluoropolymer used within the moist slurry course of, is also probably impacted by the identical rules.
Fluoropolymers on the whole are important to lithium-ion batteries, and so they’re important for us to transition to a clear power surroundings. So, we need to be companions within the regulation to make it possible for the rules deal with the considerations, and that these merchandise are manufactured in a accountable method, and we’re dedicated to doing each issues.
This text first appeared in Situation 69: July-September 2024 – Subscribe now.